
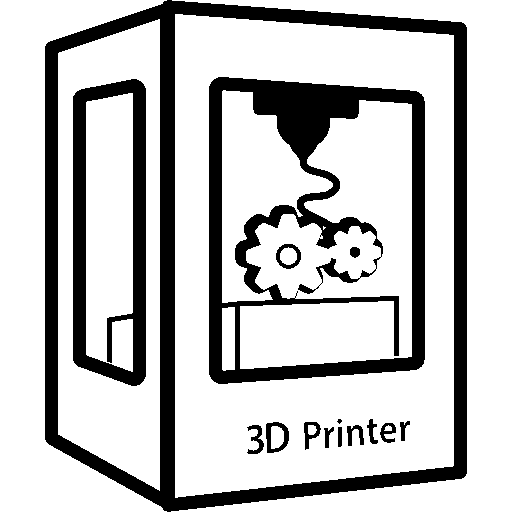
- If micro stepping varies that much then FDM printers (and CNC machines) wouldn’t have worked so well. Also, you can tune the micro steps, if you need 410 steps to move exactly 10mm instead of the default 400, just change it. (I just pull a random number btw, it’s been at least 5 years since I touched my Marlin firmware)
- If you’re familiar with coffee grinders, they’re basically using thread to adjust distance between 2 burrs. Even there (mid to upper-mid range ones) can’t guarantee the same grind size on the same setting for different unit of the same model, eg. setting 11 on grinder A will have slightly different result compared to another unit of grinder A on setting 11. Can it be done? Yes, one example is Commandante, that is a $300 hand grinder.
Tight tolerances will exponentially skyrocket production cost, period.
Is it possible? Yes. And you’ve mentioned stability could be an issue. I’ll add that if you count your time and wasted plastics to test the thickness, infill, etc. I think it’ll cost more than just buying the extrusion.
That said, if you already have core xy printer, you can start testing by replacing the frame with a printed parts. Starts with the vertical ones.