
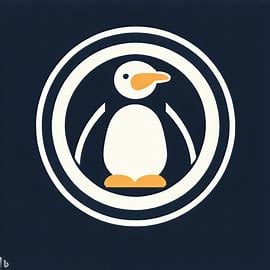
OBS can use NVENC, though IIRC it needs to be built with support enabled, which may not be the case for all distros’ package managers.
OBS can use NVENC, though IIRC it needs to be built with support enabled, which may not be the case for all distros’ package managers.
Unfortunately proprietary professional software suites are still usually better than their FOSS counterparts. For instance Altium Designer vs KiCAD for ECAD, and Solidworks vs FreeCAD. That’s not to say the open source tools are bad. I use them myself all the time. But the proprietary tools usually are more robust (for instance, it is fairly easy to break models in FreeCAD if you aren’t careful) and have better workflows for creating really complex designs.
I’ll also add that Lightroom is still better than Darktable and RawTherapee for me. Both of the open source options are still good, but Lightroom has better denoising in my experience. It also is better at supporting new cameras and lenses compared to the open source options.
With time I’m sure the open source solutions will improve and catch up to the proprietary ones. KiCAD and FreeCAD are already good enough for my needs, but that may not have been true if I were working on very complex projects.
Cute cat! Nevermore and Bentobox are two super popular ones.
Since you’re running an E3 V2, first make sure you’ve replaced the hotend with an all-metal design. The stock hotend has the PTFE tube routed all the way into the hotend, which is fine for low temp materials like PLA, but can result in off-gassing at higher temperatures such as those used by ASA and some variants of PETG. The PTFE particles are almost certainly not good to breathe in during the long term, and can even be deadly to certain animals such as birds at small quantities.
In my experience doing a bit more than 10% can be helpful in the event of underextrusion, plus I’ve seen it add a bit more rigidity. But you’re right that there are diminishing returns till you start maxing out the infill.
4 perimeters at 0.6mm or 6 at 0.4 should be fine.
Yeah, I agree. In the photo I didn’t see an enclosure so I said PETG is fine for this application. With an enclosure you’d really want to use ABS/ASA, though PETG could work in a pinch.
I also agree that an enclosure (combined with a filter) is a good idea. I think people tend to undersell the potential dangers from 3D printing, especially for people with animals in the home.
All good, it’s still something to keep in mind (especially if OP thinks about enclosing their printer in the future). Thanks for your comment!
IMO heat formed from stress will not be a big deal, especially considering that people frequently build machines out of PETG (Prusa’s i3 variants, custom CoreXYs like Vorons and E3NG). The bigger problem is creep, which suggests that you shouldn’t use PLA for this part.
PETG will almost certainly be fine. Just use lots of walls (6 walls, maybe 30% infill). PETG’s heat resistance is more than good enough for a non-enclosed printer. Prusa has used PETG for their printer parts for a very long time without issues.
Heat isn’t the issue to worry about IMO. The bigger issue is creep/cold flowing, which is permanent deformation that results even from relatively light, sustained loads. PLA has very poor creep resistance unless annealed, but PETG is a quite a bit better. ABS/ASA would be even better but they’re much more of a headache to print.
It really depends on what you’re looking for. Are you just looking to learn how to print new materials, or do you have specific requirements for a project?
If it’s the former, I’d say the easiest thing to try is PETG. It prints pretty reasonably on most printers though has stringing issues. It has different mechanical properties that make it suitable for other applications (for example, better temperature resistance and impact strength). It’ll be much less frustrating than trying to dial in ABS for the first time.
ABS and TPU are both a pretty large step up in difficulty, but are quite good for functional parts. If you insist on learning one of these, pick whichever one fits with your projects better. For ABS you’ll want an enclosure and a well ventilated room (IMO I wouldn’t be in the same room as the printer) as it emits harmful chemicals during printing.
A filament dryer was honestly the single biggest improvement to my printer’s quality. I’d definitely recommend getting one. Wet filament is so frustrating to print.
I’ve tried Overture, Creality, and Inland (all black though, not transparent) and Overture printed the best for me (at least for functional parts where I cared about print quality and tolerances). Inland’s PETG+ and High Speed PETG was even better though.
I don’t know the architecture of AI accelerator in Ryzen processors but I do know a fair amount of image deblurring and denoising tools run on the neural engine on Apple Silicon. The neural engine is good enough for a lot of tasks, provided that your model only uses relatively simple operators and doesn’t need full precision.
What I do have an issue with is new users that try and have problems and immediately start whinging that “FreeCAD isn’t like what I know. And it needs to be like my favorite” Those are the lazy people that can’t be bothered to learn something new. And they should either expend the effort to learn or go back to whatever they were using
I think that’s fair, but most criticisms of FreeCAD from people coming from other CAD packages rather fall into your latter category that you mention here:
But if you have given FreeCAD, (or ANYTHING new in life), an honest try and you can’t get the hang of it or simply don’t like it.
I don’t think we’re actually disagreeing in principle, just on what we perceive as the common criticisms of FreeCAD. Normally, I’ve seen people from other CAD programs get frustrated at limitations within FreeCAD or needing to work around bugs in ways that slow them down. For example, FreeCAD previously was unable to cope with multiple geometries being contained in a single sketch (I believe 1.0 now supports multiple extrudes from different sketch regions, but previously FreeCAD would throw an error), which made modeling less efficient for those coming from programs like Solidworks where this feature exists. Throw other issues like toponaming into the mix and it’s no surprise people from other CAD programs tried learning it, got frustrated (since their baseline was better than what FreeCAD could offer) and moved on.
I agree that criticizing FreeCAD for having different workflows than other CAD programs is a bit silly, though. I don’t really care what the exact workflow is as long as it 1) works and 2) is fast, and for me FreeCAD 1.0 (and previously Realthunder’s branch) ticks all the boxes there.
I appreciate the respectful discussion!
I do think the point about all CAD packages having failure paths is a little overblown. Yes, you can definitely get proprietary CAD to break but in my experience (at least with Solidworks and Fusion), it usually requires much more complex parts than FreeCAD parts. Post 1.0 the situation is definitely better though.
You’re right that users should try following best practices from day one, but realistically most users are not going to learn everything correctly automatically. They might use an out of date tutorial, or might have just learned by tinkering themselves.
The point I was trying to make was that because FreeCAD operates differently than other CAD programs do to one another and because it’s generally a bit more brittle and demanding of the user, I can’t say I blame anyone for not wanting to switch to it if they already have a CAD program they’re proficient with. You could call it being lazy, but from a practical standpoint there isn’t necessarily a ton to gain for a relatively large amount of time investment required to be capable of using it.
I really hope FreeCAD improves enough one day in the new user experience department. I love the software and have been using it as my tool of choice for years now, but evidently not everyone thinks it’s worth the time investment.
The main benefit I think is massive scalability. For instance, DOE scientists at Argonne National Laboratory are working on training a language model for scientific uses. This isn’t something you can do on even 10s of GPUs for a few hours, like is common for jobs run in university clusters and similar. They’re doing this by scaling up to use a large portion of ALCF Aurora, which is an Exascale supercomputer.
Basically, for certain problems you either need both the ability to run jobs on lots of hardware and the ability to run them for long (but not too long to limit other labs’ work) periods of time. Big clusters like Aurora are helpful for that.
I’ll mention this fix is aimed at mitigating toponaming primarily for sketch attachment. Some features still struggle with toponaming, namely chamfers and fillets. But in any case, it’s a massive step forward and makes FreeCAD much easier to recommend! Until now I’ve been using Realthunder’s fork since toponaming was such a headache to resolve manually.
I think that’s a little unfair. The bigger issue IMO is that FreeCAD doesn’t quite share the same workflow as other (proprierary) CAD packages, so someone coming from proprietary CAD also needs to unlearn habits that were previously fine but now potentially harmful. For example, adding chamfers and fillets in FreeCAD pretty much should only be done at the end to avoid toponaming issues, which is less of an issue in other packages.
One of the big changes in my opinion is the addition of a “Smart Dimension” tool where the system interprets and previews the constraint that you want to apply instead of requiring you to pick the specific constraint ahead of time(almost identical to SOLIDWORKS), and the ability to add constraints such as length while drawing out shapes (like Autodesk Inventor, probably also Fusion but I haven’t used that). It makes the sketcher workflow more like other CAD programs and requires a little less manual work with constraints.
Hmm, that actually sounds like a bug. I haven’t seen that on my end (once I set the locations of options in my toolbars they stay there, even after restarts). You may want to report that on their issue tracker. Sorry that you’re having a rough experience!
I agree with your thoughts. I hate what Bambu has done to the industry in terms of starting a patents arms race and encouraging other companies to reject open source, but I do love how they’ve pushed innovation and have made 3D printing easier for people just looking for a tool.
I hope the DIY printers like Voron, Ratrig, VzBot, and E3NG can continue the spirit of the RepRap movement.